
How 3D printing lowered the threshold for innovation at Teleste
At Teleste, we have set out to create an open and free working environment where our employees have the psychological safety to bring up new ideas and suggestions to improve processes, tools and their daily work. 3D printing has taken this philosophy to a very tangible level. It has enabled us to create tools that were previously not financially feasible to develop let alone possible to create with traditional fabrication methods.
Teleste’s Manufacturing Engineering & Technology (MET) team’s key strategic focus area is to retrain and upskill our existing workers in order to be able to not only adapt but to drive the future of our industry. One of our in-house focus areas for MET has been 3D printing. The main aim of our venture into 3D printing has been to create tools and jigs that help our employees to better perform their daily tasks. Two of our MET team members with an intrinsic motivation and interest in 3D technology were selected to resolve skill gaps related to 3D printing. The team was immediately exhilarated to channel their own enthusiasm into their work, which kicked off the project into a running start. Within a very short time period, we had a team that was fully capable of conceptualizing and designing 3D models in-house, in combination with relationships with the 3D printing partner companies.
From an idea to concept to function in less than a week
In the past, developing new tools was heavily tied in with painstaking, time-consuming and costly processes that may involve metal prototyping and expensive fabrication, which simply raised the threshold of getting new ideas off the ground. We quickly discovered that 3D printing is a game-changer in this regard. From the idea to fabrication process time diminished from several weeks or more to often less than a week. In practice, an idea for a tool or jigs can be physically realized by the following week. The time and cost-efficiency of the process feeds into our creativity, where nothing is off the table. One of the factors that 3D printing technology has enabled us to do is lower the threshold of innovation. The trial and error process is no longer costly and time-consuming, so the technology enables us to take risks, experiment, and importantly iterate on our previous tools and products.
Cataloging everything for better decision making
Following our 3D printing trials, we have built up a continually growing catalog of 3D printed tools, jigs, and components that can be quickly utilized for reprints and iterative development. The catalog features detailed images, 3D models, measurements, and material information for each of our creations. We are now able to quickly reference the catalog for the printing time and costs associated with specific tools and designs.
Our 3D printing team is constantly updating itself with the latest printing materials, and new techniques. They also provide regular debriefs to the entire MET team to get everyone up to speed on what is possible to do and what are the latest materials that we can utilize. Overall, our endeavor into 3D printing has been a major success. It has enabled us to create tools that help us carry out our daily routines more effectively and in a way that makes our employees’ work days more productive and enjoyable. The project has also allowed our employees to channel their passions into what they do, and this has not only been an effective driver for innovation but also contributed to the enjoyment and wellbeing of working at Teleste.
Marko Uutela
Marko Uutela
I’m currently heading Operations, Logistics & Sourcing for Teleste’s Public Safety and Mobility business. See my LinkedIn for more information.
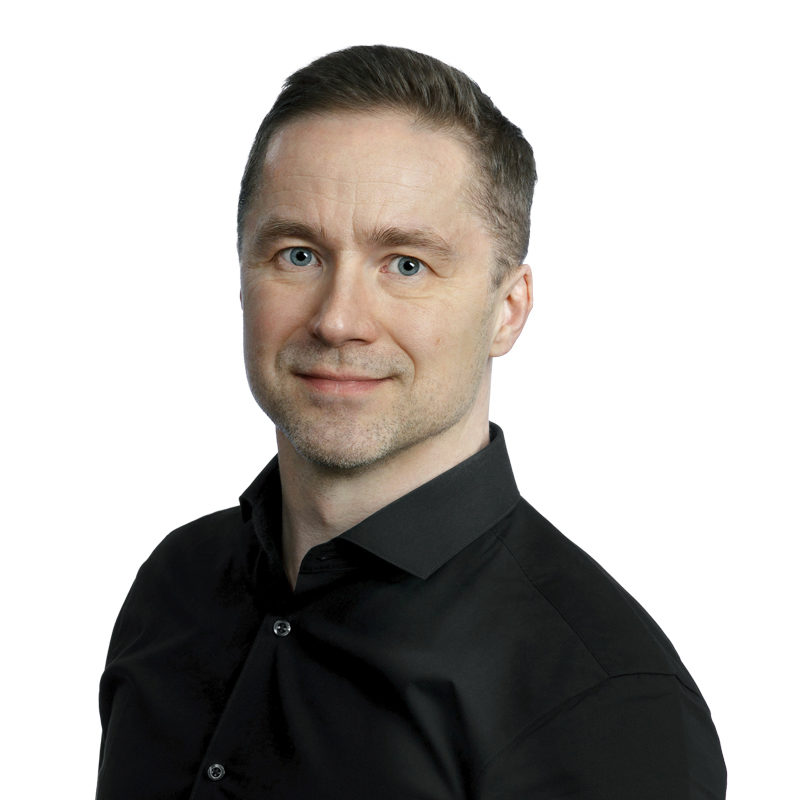