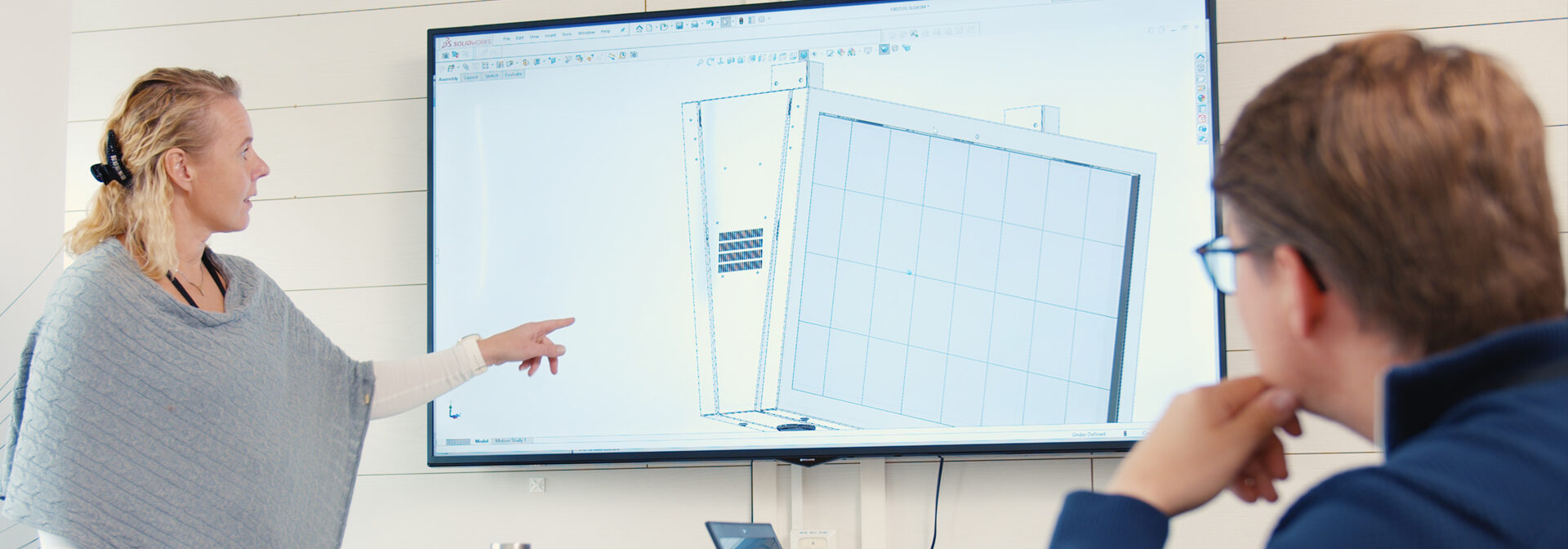
Design FMEA to support design for reliability action
At Teleste, our primary objective is to ensure high customer satisfaction by meticulously incorporating customer needs to our design practices. A pivotal factor in achieving this goal is product reliability. Our products are engineered to be long-lasting, with the expectation that they will operate maintenance-free for years in a variety of environments
During product development, various measures are undertaken to ensure the desired level of reliability for a product. Design FMEA (Failure Modes and Effects Analysis) stands out as a valuable tool that can be employed, even in the early stages, to systematically assess and address potential technical risks embedded in the design. Importantly, Design FMEA can be conducted even when the design still remains “on paper”, making it easier to implement any necessary modifications.
Design FMEA sessions start with careful examination of the product in development, encompassing a comprehensive review of its requirements, functions, and interfaces with other devices. Furthermore, a thorough analysis of the anticipated usage environment will be carried out, and existing similar products in operation are mapped to gather valuable field data that enhances the analysis. This initial phase plays an essential role in understanding both the product itself and the environment where it is expected to work.
Once the product is dissected into functional blocks, failure modes are identified, and the mechanisms and consequences of these failures analysed. A formal FMEA study also rates different failure scenarios based on their severity (S), occurrence (O) and detection (D). These ratings can then be used for the calculation of a Risk Priority Number (RPN), which helps pinpoint and prioritise the most impactful failure scenarios.
Design FMEA is an evolving document that doesn’t conclude with its initial iteration. Once the recommended actions have been implemented, it’s imperative to review the analysis and recalculate the RPN. Whenever design changes are introduced, the design FMEA should be revisited to incorporate these alterations. Furthermore, when a new version or next-generation product is developed, the design FMEA should be reassessed for the updated components.
Consequently, Design FMEA serves as a valuable tool for revealing potential failure points within the design, enabling necessary corrections, facilitating the development of testing procedures, refining work instructions, and enhancing production controls, among other benefits. The primary advantage of this analysis lies in its ability to provide a comprehensive understanding of potential risks within the product, allowing for proactive preparation. Even if it’s not possible to mitigate all risks, this enhanced awareness equips us to better anticipate and address challenges in the future.
How do you envision integrating Design FMEA or other risk assessment practices into your own design and development processes?
Kati Kokko
Kati Kokko
I am RAM and LCC specialist at Teleste’s Rolling Stock Manufacturers / Rail Information Solutions organization. I joined Teleste in May 2020, and I have wide experience in electronics reliability and electronics industry. I have experience in research at university as well as leading reliability team in electronics industry. I hold a Doctor of Technology degree in electronics. You can find more about me in my LinkedIn profile.
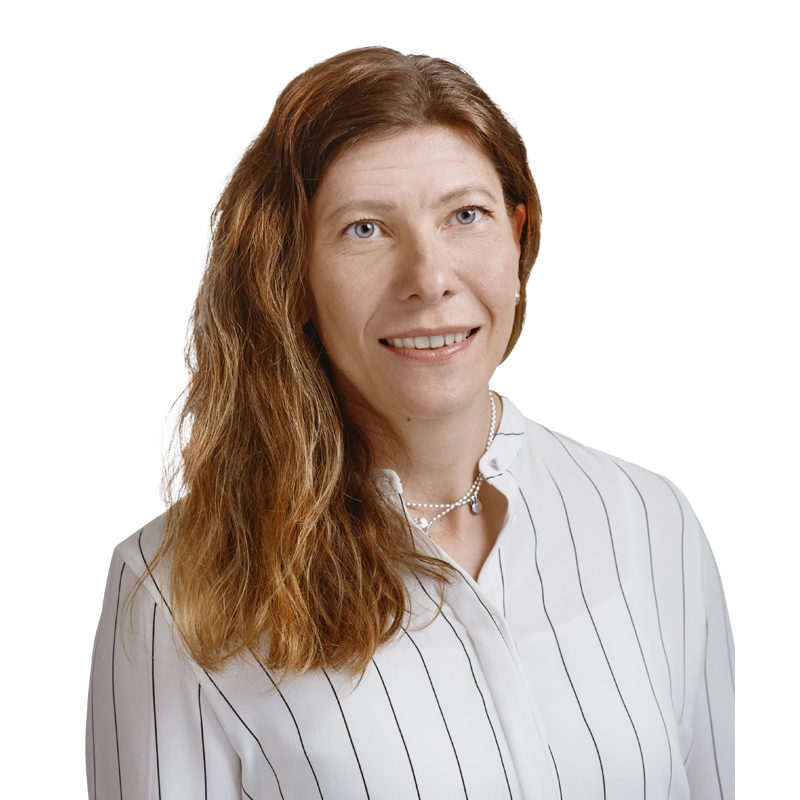